A version of this article was first published in the Fall 2024 Issue of NAIOP’s magazine.
Demand for new, single-user warehouses is still strong. But thanks to a confluence of trends, some owners have compelling reasons to consider subdividing their industrial assets to accommodate the needs of multiple lessees.
For starters, fewer occupiers are leasing the largest assets— so-called mega warehouses of 1 million square feet or larger. According to research from CBRE, there were 43 industrial lease transactions of at least 1 million square feet in 2023, down from 63 such deals in 2022 and 57 in 2021.
Cushman & Wakefield’s Q1 report on the U.S. industrial-sector notes that “these larger deals are taking longer to transact, primarily due to cost-containment measures related to economic uncertainty and a general slowing in consumer demand for goods.”
Meanwhile, the availability of smaller-format industrial spaces has reached historic lows, according to a March 2024 report by CoStar, which noted that smaller industrial properties “have increasingly stood out as one of the best-performing categories of commercial real estate” owing mainly to their “insulation from supply-side risk.”
Why is the supply so constrained? One factor, according to CoStar, is that developers of newly completed, unleased big-box distribution centers are generally unwilling to subdivide them to tenants smaller than 25,000 or even 50,000 square feet. That makes sense. A brand-new, large-format DC is a major investment; the developer of such an asset is likely to exercise patience before sinking more money into the building and making major changes to it.
But at the same time, as CoStar observes, “vacancy rates among small industrial properties remain near all-time lows.” The trend is visible across many different markets. CoStar’s research team cites Dallas-Fort Worth, where “the current 6.1% availability rate for small industrial properties is well below the 8.7% level recorded in the market 10 years ago. Similarly, the median time to lease for spaces smaller than 10,000 square feet in Dallas-Fort Worth is 3 1/2 months, down from the median time to lease of five months recorded 10 years earlier.”
A Logical Conclusion
For owners of older, larger assets—especially industrial buildings that are vacant or on the cusp of becoming so—the aforementioned trends mean that finding a single replacement user could be more difficult than in the past. Meanwhile, operators with more modest space needs are clamoring to do deals.
Subdivision, in other words, could be having a moment. And anecdotally, at least, interest in these projects does appear to be growing.
In some cases, landlords take the initiative to subdivide warehouses. They might create separate entrances, install partitions, and adapt the layout to accommodate multiple users. This approach allows the landlord to attract a diverse range of tenants. Alternatively, a long-term tenant with excess space can sublease part of its area to other businesses. This arrangement allows the original tenant to retain its existing space while sharing the costs and benefits of the property.
Shifting from a single primary user to multiple users will pose challenges. This article addresses a few key considerations for those interested in subdividing industrial buildings.
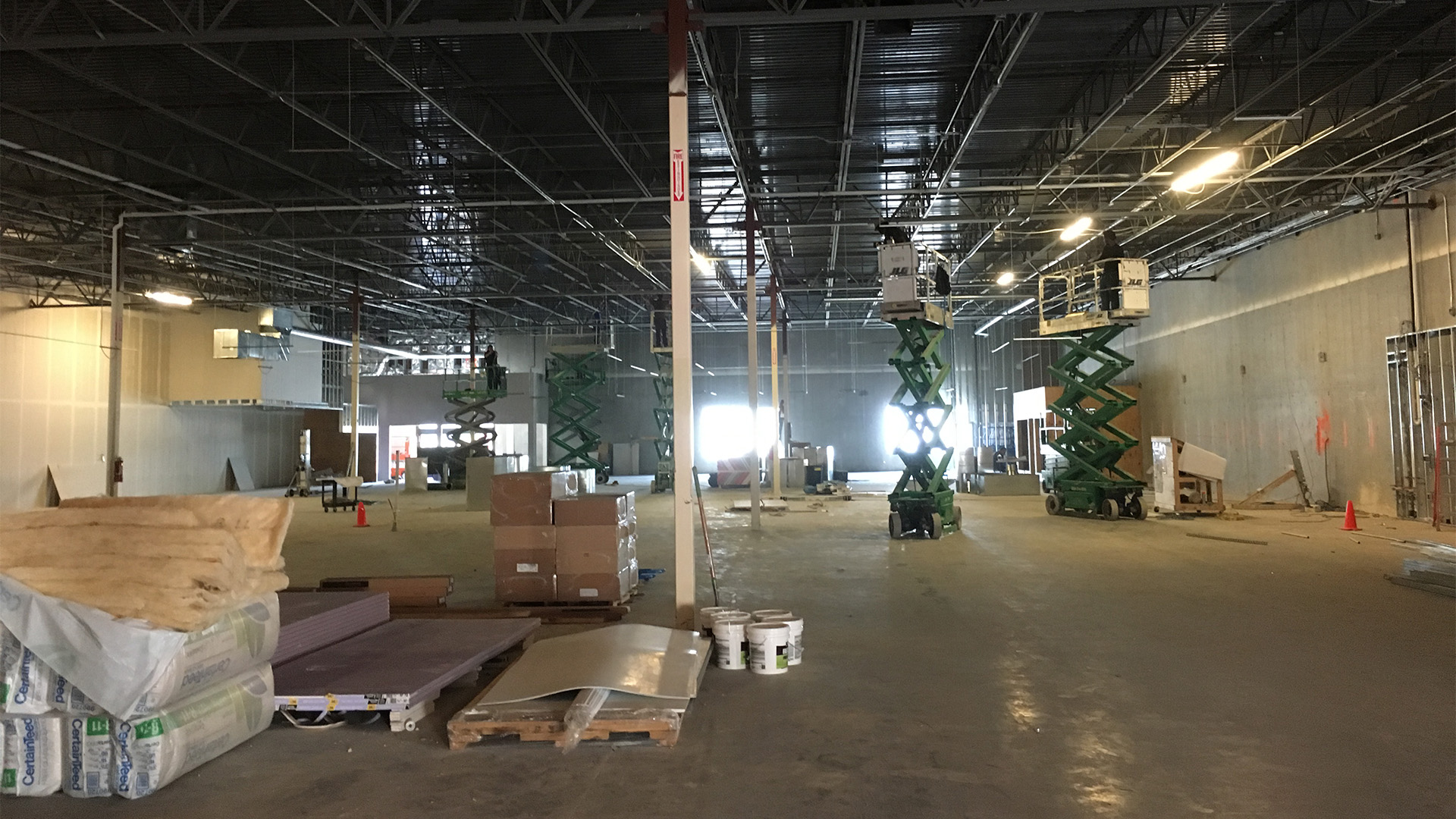
Rethinking MEP
Industrial users have varying needs for water, electricity and HVAC. When embarking on a subdivision project, it’s important to pay close attention to the allocation of mechanical, electrical and plumbing (MEP) systems. Each individual space must be properly submetered, with each tenant having independent controls.
The trends toward automation and data centers make utilities particularly important. While the density of automated storage and retrieval systems (ASRS) means that some tenants will not need as large a space as in the past, their continuous use of this energy-intensive equipment could end up increasing the building’s overall power requirements. Data centers are notoriously power-hungry.
Lessors or sublessors need to answer the following questions well before the lease is inked and buildout begins:
- Will the building have adequate electrical service to accommodate the jump in usage that could result from ASRS or the introduction of a data center?
- If a service upgrade is needed, will the local electrical utility allow it based on existing grid constraints?
- How could co-tenants be affected if an “energy hog” ends up gobbling more electricity than planned?
Upcycling the New Spaces
In some cases, the subdivision project will involve upcycling portions of the building. Typically, that means making improvements to align with a new tenant’s business model, comply with updated codes, or enhance the competitiveness of an unleased asset. Additionally, rezoning can provide significant benefits by increasing property value and allowing for a more diverse and attractive tenant mix. Examples of beneficial rezoning could include:
- eliminating or updating a planned development (PD) and/or its associated setbacks or other restrictions;
- moving to a medical research use;
- adding heavier manufacturing zoning permissions; or
- broadening the available scope of commercial service users.
This overall strategic approach ensures that the building remains versatile and appealing to a broader range of potential tenants.
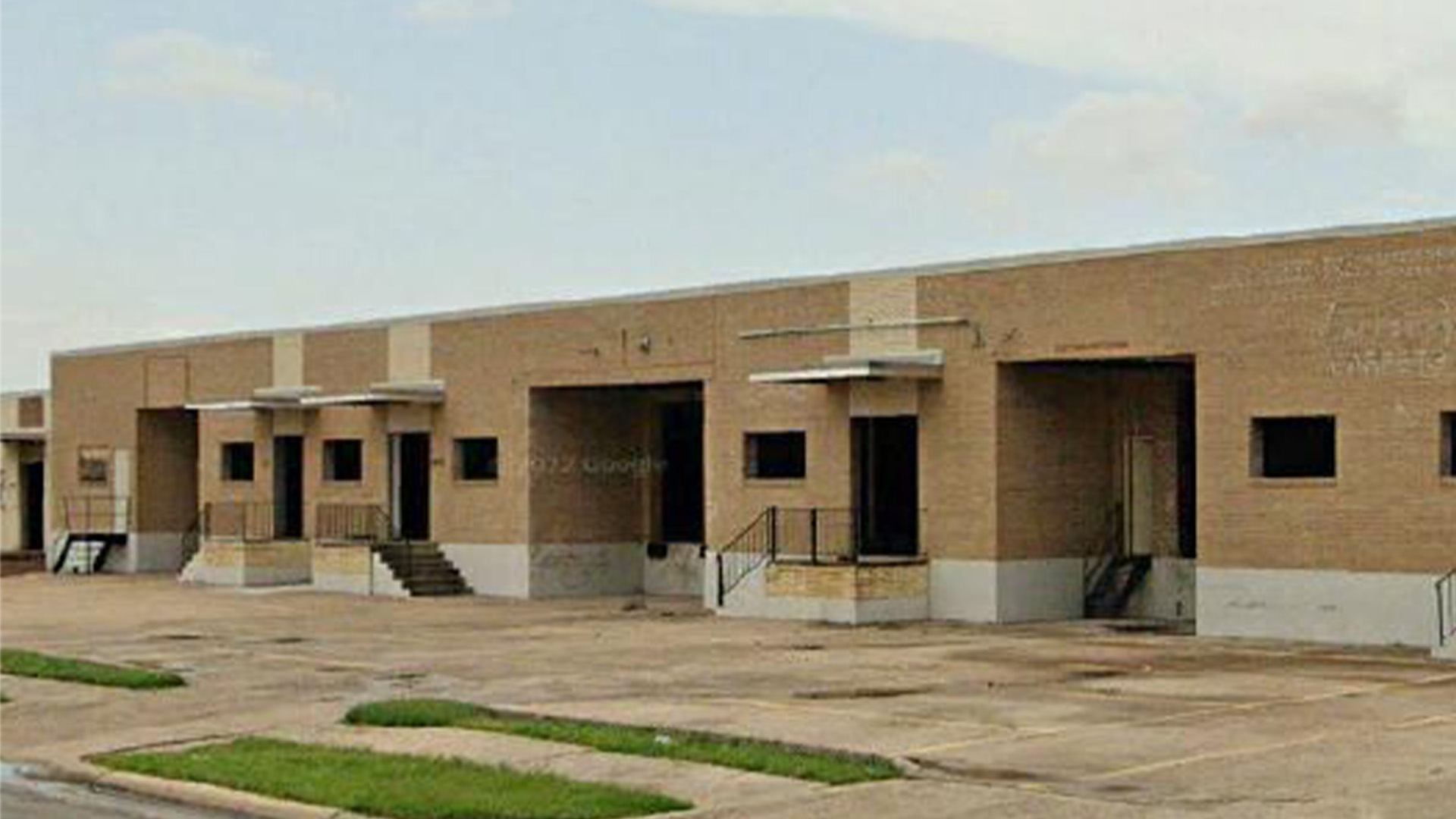
A Project in the Pipeline
In Dallas, a 1960s-era 75,000-square-foot warehouse is now in the planning stages of a subdivision project. Due to the lack of modern amenities and being badly damaged by a 2019 tornado, it could not compete with nearby industrial assets.
The owner now aims to bring the warehouse up to current standards, inside and out, and to provide all-new, independent office amenities for each newly subdivided space (four in all). The substantial project will require conforming to modern development codes and correcting ADA-access concerns.
Utilities will need to be subdivided and submetered for the four new spaces. The addition of accommodations for modern, more energy-intensive users could mean that the entire building’s electrical service will require an upgrade. The building envelope also will need to be addressed with the introduction of upgraded mechanical systems and environmental controls.
By making these changes, the owner stands to secure multiple tenant lease agreements, restoring value to the property. How much will it cost? Approximately $450,000 per the current pro forma. After repairs, the developer expects annual internal rate of return (IRR) of more than 500%.
Use-Specific Upcycling
In other cases, tenant- or use-specific upcycling can be required as part of subdivision projects. For example, as part of a long-term lease agreement with a smaller-format industrial tenant that plans to install and use AS/RS (Automated Storage and Retrieval System), owners of older buildings might need to make some significant alterations that enable the equipment to operate efficiently.
In particular, floors must be perfectly flat. Over a given stretch of 50 to 100 feet of horizontal surface, even deviations as minute as half an inch could reduce the robots’ efficiency as they zip along a predetermined path. The engineering team might need to X-ray or pull core samples from concrete floors to ensure they are adequately and uniformly thick throughout. (Thickness has a direct correlation to the bearing capacity of the slab, which needs to match the requirements of the new racking and automation components.) Lifting the roof to accommodate today’s structural clear heights might be necessary as well.
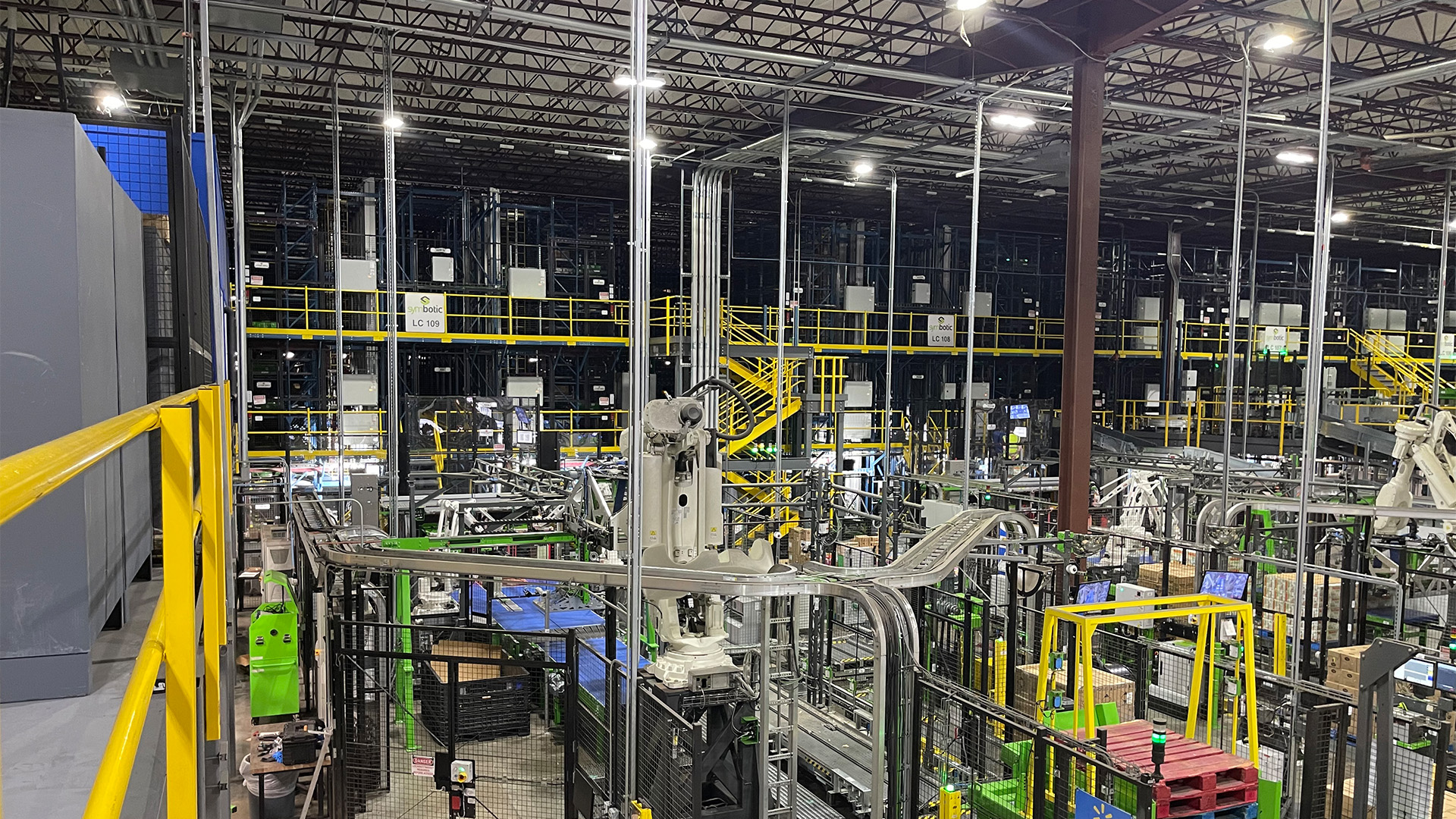
Meanwhile, the tech sector’s voracious appetite for data is creating more potential for leasing or subleasing deals with these operators. True enough, tech giants seeking to take machine learning and large language models to the next level tend to occupy massive buildings and complexes. However, there is a whole universe of smaller data center users—good candidates for subdivided spaces.
Indeed, colocation data centers are essentially subdivided industrial buildings. In downtown Dallas, one 80,000-square-foot complex run by IT solutions provider Flexential bills itself as “five data centers, one location.”
In a June 2023 report (“Why Smaller Data Centers Are Taking Off”), JLL points to demand from smaller “edge data centers.” These facilities “bring computing capability geographically closer to those users situated farther away from the heart of the cloud” and “have a smaller capacity between 500 kilowatts to 2 MW.”
The industrial spaces used by data centers typically must be kept within controlled temperature and humidity ranges, with precise approaches to ventilation. Many older industrial buildings were designed to maintain less-than-comfy temperatures of 80 or 90 degrees Fahrenheit. Introducing climate controls and better ventilation could require a detailed analysis of the building envelope and reinsulation of existing panels and the roof, along with assessments of rooftop mechanical equipment and the required addition of structural supports for the heavier HVAC system.
Adapting a subdivided space for another high-growth use—cold storage—often requires the introduction of thermal breaks between freezer boxes and the parts of the building that surround them. Typically, the floor must be torn out and replaced so that freezers can be properly isolated. Otherwise, cold can leach out from the boxes into the concrete, causing condensation and ice. The new space might also need to be altered or expanded to provide adequate room for those associated refrigeration systems.
In general, developers engaged in upcycling can expect per-square-foot costs along the lines of:
- $1.84 for concrete sealing and striping;
- $5.40 for roof penetrations, doors, glazing, drywall and ceilings;
- $1.70 for paint;
- $2.96 for plumbing;
- $2.43 for HVAC; and
- $3.60 for electrical.
The incentives can make these changes well worth the effort: An older, class “C” industrial building can easily make the jump to “B” after a subdivision project, so long as the location is good. In the Dallas market, according to PropertyShark listings, that could yield an annual rent increase cap from $14 to $19 per square foot.
Revisiting Fire Safety and Parking
Subdividing a warehouse also requires a careful second look at the building’s entire fire safety and suppression system. The design may involve creating a raft of new walls, hallways, doors, and entrances and exits, some of which are likely to see substantial pedestrian traffic. Based on existing codes, manufacturer specs and fire-safety best practices, the engineering team will need to make sure that doors in any MFL (maximum foreseeable loss) walls can automatically drop to close off some of these spaces if the fire-suppression system is triggered.
In many cases, subdividing a warehouse and bringing in new tenants will add complexities —additional cars, trucks, containers or pedestrians — to the site’s overall operation. From the standpoint of civil engineering, parts of the building or site might need to be redesigned to maximize site-flow efficiency and safety.
Changes to parking ratios and utilization of roadway infrastructure also will necessitate conversations with the municipality and, potentially, other community stakeholders.
ESG Upgrades
Industrial occupiers are increasingly focused on ESG (Environmental, Social, and Governance), from slashing carbon consumption to giving employees healthier, safer and more comfortable work environments. As part of a subdivision project, owners could consider taking advantage of tax incentives and grants designed to promote energy efficiency and decarbonization. Examples include installing solar panels, new insulation, Level 3 fast chargers for electric vehicles, or on-site hydrogen generation for fuel-cell forklifts.

Introducing high-quality common spaces and amenities to the newly created, smaller spaces can be a selling point. Industrial tenants are now more likely to give their employees larger break rooms and better-located bathrooms.
Industrial in the Reinvestment Era
As assets age and the pace of development cools, it is natural for reinvention, reinvestment and downsizing to become a focus. Subdivision might not be the best option for every asset, but it certainly can be worth a second look, especially if vacancy looms or has become an issue for the property. The world of industrial real estate is becoming increasingly diverse. While massive, single-user warehouse distribution centers will continue to be a central part of the picture, demand is rising among smaller users, too. Leveraging a subdivision strategy to meet these operators’ needs could be a smart way to achieve full occupancy and higher ROI.
Marc Jennings, NCARB, is Vice President of Industrial and Logistics at HFA Architects + Engineers. Andrew Akerhielm, AIA, NCARB, LEED AP BD+C, is a Senior HFA Architect and Client Lead.