In a trend that should surprise no one, hybrid shopping habits (meaning a mix of physical and online shopping) have begun to steadily gain popularity as shoppers wish to curate their own ideal shopping journeys. (Hybrid shopping is the primary shopping method for more than 27% of consumers, with 37% identifying as Gen Z—which is more than any other generation.) What hasn’t increased, however, is the availability of a reliable workforce. More and more companies are finding it harder to maintain or retain workers while simultaneously moving product to customers faster than ever—forcing companies to make tough choices—by either slashing operating hours or worse, closing their doors altogether. To overcome this challenge, some larger retailers are willing to adopt new technology and reformat their ways of working to make up for the shortage of available skilled laborers. Enter: Automated Distribution Centers.
In this article, we’ll dive deeper into why this unique adaptation of the Distribution Center of years past may be the right move for more and more retailers; plus, we’ll rely heavily on the expertise within the disciplines that need to come together to make this dream a reality.
New Sites: Key Considerations and Challenges by Discipline
Working with automation companies, and the technology that comes with it, often requires many design considerations on the front-end, especially when embarking on a ground-up automation project. Change orders, redesigns during construction, and more can derail any project, but can have a huge, and often costly impact on automated distribution centers. As the project moves through the design and construction lifecycle, many disciplines must lean in with their expertise to coordinate a successful ground-up automated distribution center. We’ll look at some of the specific considerations below by discipline.
Structural Engineering
From a purely structural perspective, one of the most crucial components is the underlying concrete slab. For many robotics systems to function as designed, the slab must be poured very flat, be structurally sound, and oftentimes must be reinforced. This layers into each specific automation company’s specific requirements and specifications—they generally call the shots.
Structural Challenges
The most significant aspects for consideration ironically concern both the top and bottom of the building, and many questions must be considered early on.
- First and foremost, is the concrete slab sufficient to maintain the degree of flatness and levelness required for automation systems to function properly?
- Does the slab need to be thicker than normal to allow the automation system to be adequately and safely anchored to the slab? Keep in mind that the slab must also allow for moving the system to its final location during the construction process, as well.
- Ceiling heights and clearances must be planned well ahead of time and double checked with the automation manufacturers to make sure they leave adequate space for the automation systems planned for the space.
Architectural
What an automated distribution center lacks in traditional architectural design, it more than makes up for it in design coordination. Architects oversee all aspects of the project design and function as the main point of contact for clients, client consultants, allied disciplines, and MHE (Material Handling Equipment) vendors. They are responsible for coordinating and facilitating communication between all disciplines to maintain project schedules and milestones. As MHE systems are often cutting-edge proprietary design, the architect is often called upon as a building code expert to verify that life safety is not sacrificed for the sake of system design efficiency. While administration-driven, the role of an architect is crucial to the success of the project.
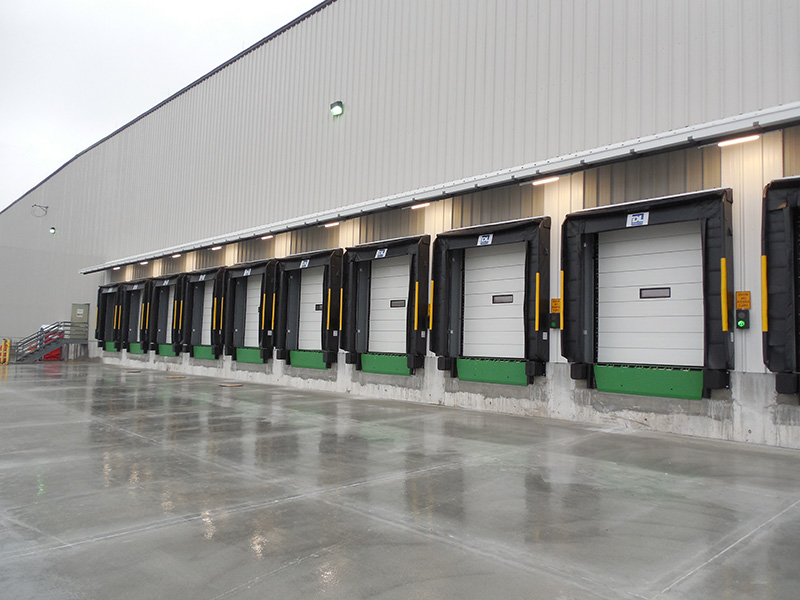
Civil Engineering
For Distribution and Fulfillment Centers in particular, thought must also be given to the flow and traffic pattern of the parking lot and receiving docks.
- Can semi-trucks get in and out easily?
- Is there enough room for distribution vehicles and the vehicles of employees working within the building?
Another qualification to consider when picking an adequate site for a distribution center is pinpointing a site with ease of access to a main thoroughfare or highway for distribution and semi-truck traffic.
Mechanical, Electrical, Plumbing & Refrigeration (MEPR)
Power and energy needs must be considered first and foremost in both adapted and new buildings, MEPR impacts from automation are often greater than typical warehouse demands.
MEPR Challenges
- If you are implementing robotics systems, the building needs to be conditioned and outfitted with airlocks to control the humidity within the building. What kind of ventilation system is needed to ensure adequate air flow? Does the equipment require special temperature conditioning for the space?
- This is an especially important consideration where robotics is concerned, because they will not work properly if confronted with unwanted condensation from high humidity levels within the building.
- Are there any cooler or freezer spaces in the layout? If so:
- How and where should the equipment be installed?
- How will the placement of this equipment affect the building structure?
- Is there adequate space?
- What types of refrigerants will be used?
- How will the refrigeration racks need to be set up?
Fire Protection
Fire protection is easily one of the most important, yet often overlooked, aspects of automated distribution centers. From the onset of a project of this caliber, fire protection engineers and the insurance provider must have conversations about the type of automation system used, the commodities that will be stored, and the final storage arrangement that will be utilized. Each of these items will affect a potential fire's burn characteristics, and therefore effect which fire protection solutions should be implemented. Every step of the way, the fire protection team must maintain close contact with the entire team involved in the project because small changes can have large financial and life safety impacts due to fire protection requirements needed later in the project.
Fire Protection Challenges
- Other specifications include the presence of in-rack sprinklers:
- Are in-rack sprinklers required or should the team be looking at sprinkler protection under mezzanine spaces, as required by the building code?
- Is the ASRS (Automated Storage and Retrieval System) designed with adequate space for sprinklers?
Why Build New?
According to Jay Dacey, CEO at Integrated Builders headquartered in Braintree, MA, in his experience close to 90% of automated distribution center projects are new builds, solely because of the need for higher-than-average ceiling clearances and reinforced or thicker, flatter slabs than are commonly found in existing sites.
“If you've got a building that's got a 20-foot ceiling, you're more likely to demo it and the cost of that demolition just becomes part of your land purchase. You likely couldn't get someone to rent that space at 20 feet, especially if they are looking to develop an automated distribution center. While there are groups out there that can raise roofs in that situation, it’s often only worth the effort if the building is owner-occupied, rather than rented or leased.”
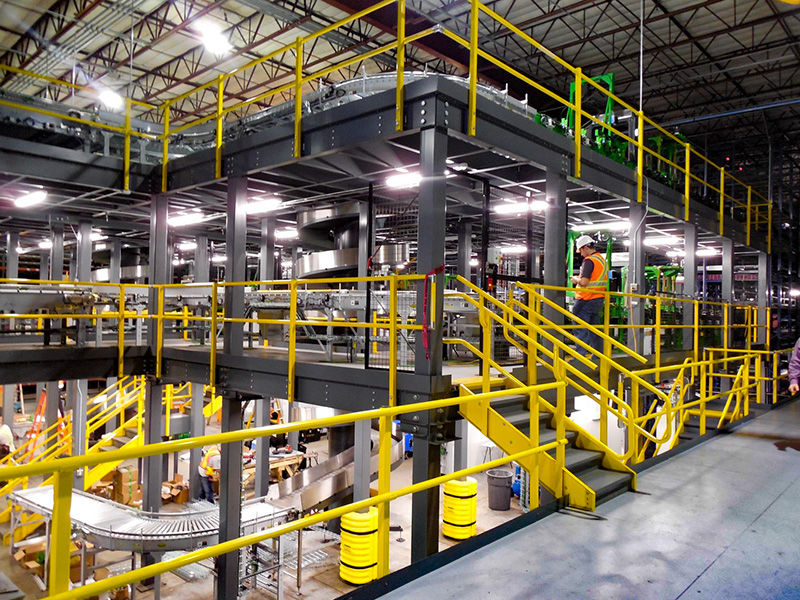
Adapting Existing Spaces: Key Considerations and Challenges by Discipline
Developing an existing site has some very clear advantages, with the largest one being securing affordable land to develop. Availability of contiguous land for developments, especially large-scale ones like automated distribution centers and other large-scale warehouse spaces is often hard to come by; and even more so if you’re seeking an option outfitted with easy access to main roads and highways and with enough room for semi-truck traffic. However, once you get past the ease of land development, many challenges can and will still arise.
Structural Engineering
The same concerns generally exist for Structural Engineering, whether the site is a ground-up or adapted site. Ceiling heights and the condition of the new or existing slab are paramount to making sure that the building is structurally sound and appropriate for the intended use and technology required of an automated distribution center. Therefore, one must ask the following questions:
- Are the ceiling clearances adequate for the robotics and/or automation systems planned for the space?
- If not, how much do they need to be raised?
- If so, is that too cost-prohibitive to the client?
The locations of vertical columns can also be a costly consideration from a structural perspective. For example, moving these columns can be both an expensive and challenging endeavor that might not be worth the headache to the client.
Architectural
One of the biggest challenges from an architectural perspective is getting ahead of the project by accessing the existing drawings so the architects can refer to them throughout the project. However, it is not uncommon to begin a project without these, which can cause problems later down the road, such as longer timelines and larger budgets. Oftentimes, the architect can become the problem solver, as many unknowns can arise during a renovation and are often uncovered during the demolition and construction process.
- A best practice to avoid the potential issues that can arise from lack of architectural drawings is to have the field team perform 3D scans that can be referred to throughout the project’s life cycle.
- Additionally, one must determine if the existing water supply accommodates a facility this large. Will a pump or tower be required?
- If so, will that be cost prohibitive for the client?
When relying on automation, employers have the unique opportunity to redefine how support spaces are integrated into the building. Obviously with fewer team members needed, break room space allocation is up for discussion, as well as things like restroom counts, number of parking spaces, and HR office space. Not only can looking at these areas reduce overhead costs, but it also allows companies to recapture and reallocate that space to the overall warehouse square footprint.
Civil Engineering
Before any other discipline touches a project of this caliber, the Civil Engineering team must deem it acceptable for the intended usage. Typically, until there is a go ahead received, other teams will not put any time or work into a project—doing so would translate into unnecessary and costly implications for a land parcel that may not be appropriate for the client.
Mechanical, Electrical, Plumbing & Refrigeration (MEPR)
From an MEP perspective, for both adapted and new sites, one must first evaluate the power and energy needs upfront, as most of these robotics systems increase both the electrical and utility load of the entire facility.
MEPR Challenges
Sometimes, backup generators or an entirely new electrical grid will be needed to support the massive electrical load these automated distribution centers incur. This is yet another project area where early coordination is crucial, necessitating a communication plan with local utility providers well in advance.
As stated in the previous section, often these MEPR challenges arise when thinking about the proper ventilation within a large warehouse space, such as an automated distribution center.
+ For instance, one must determine if there is sufficient space for any new utility equipment, like an expanded compressed air system.
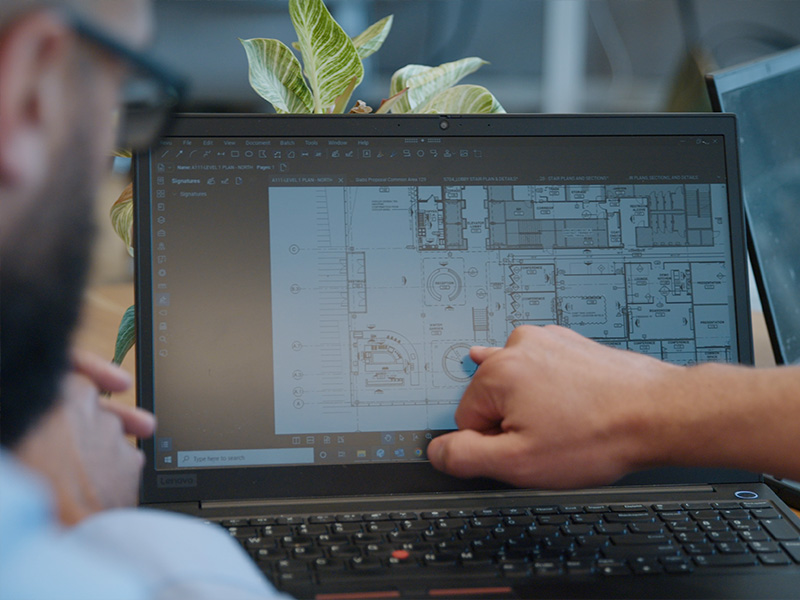
Final Thoughts
One of the most important aspects of the conversation around adapting an existing site or building new has and always will be the collaboration between all parties (this includes A+E, construction, developers, the local AHJ, and clients). This frequent coordination at every stage of the process not only helps identify problem areas early but it helps you and your clients avoid costly changes late in the construction stage.
One factor that is often overlooked is how A+E firms can “future-proof” a building. By truly partnering with their client to make sure that the building fits their needs, not just in the present, but also the future, A+ E firms can not only cut down on expensive remodeling projects in the future, but they can design with a Master Planning mindset that achieves everyone’s goals from the very beginning.
Special thanks to Andrew Akherhielm (AIA, NCARB, LEED AP BD+C), Barry Read (AIA), Brock Martin (P.E.), Garrett Small (P.E.), Giancarlo Botazzi (P.E., SECB), Jack Kucharewicz (P.E., M.ASCE), James Harte (AIA, NCARB), Miguel Purdy (P.E.), and Rob Couts (EI-AR) at HFA and Jay Dacey, CEO of Integrated Builders for their thought leadership and expertise provided throughout this article.
For more information on our work with Automated Distribution Centers, please reach out to Marc Jennings, Vice President of Logistics at HFA, marc.jennings@hfa-ae.com