Top retailers are responding to higher e-commerce sales, the supply-chain crunch and other trends by sharpening their focus on automated distribution and fulfillment. At HFA Architecture and Engineering, we believe in saving our clients time and money by bringing a similar commitment to the efficient planning and execution of automation projects as well.
Over the past seven years, our multidisciplinary architectural and engineering team has collaborated with major retailers, material handling equipment (MHE) vendors and other stakeholders to:
- Add higher-efficiency conveyor systems to existing warehouses
- Install micro-fulfillment centers (MFCs) in big-box retail stores
- Roll out AI-driven robotics in regional distribution centers (DCs)
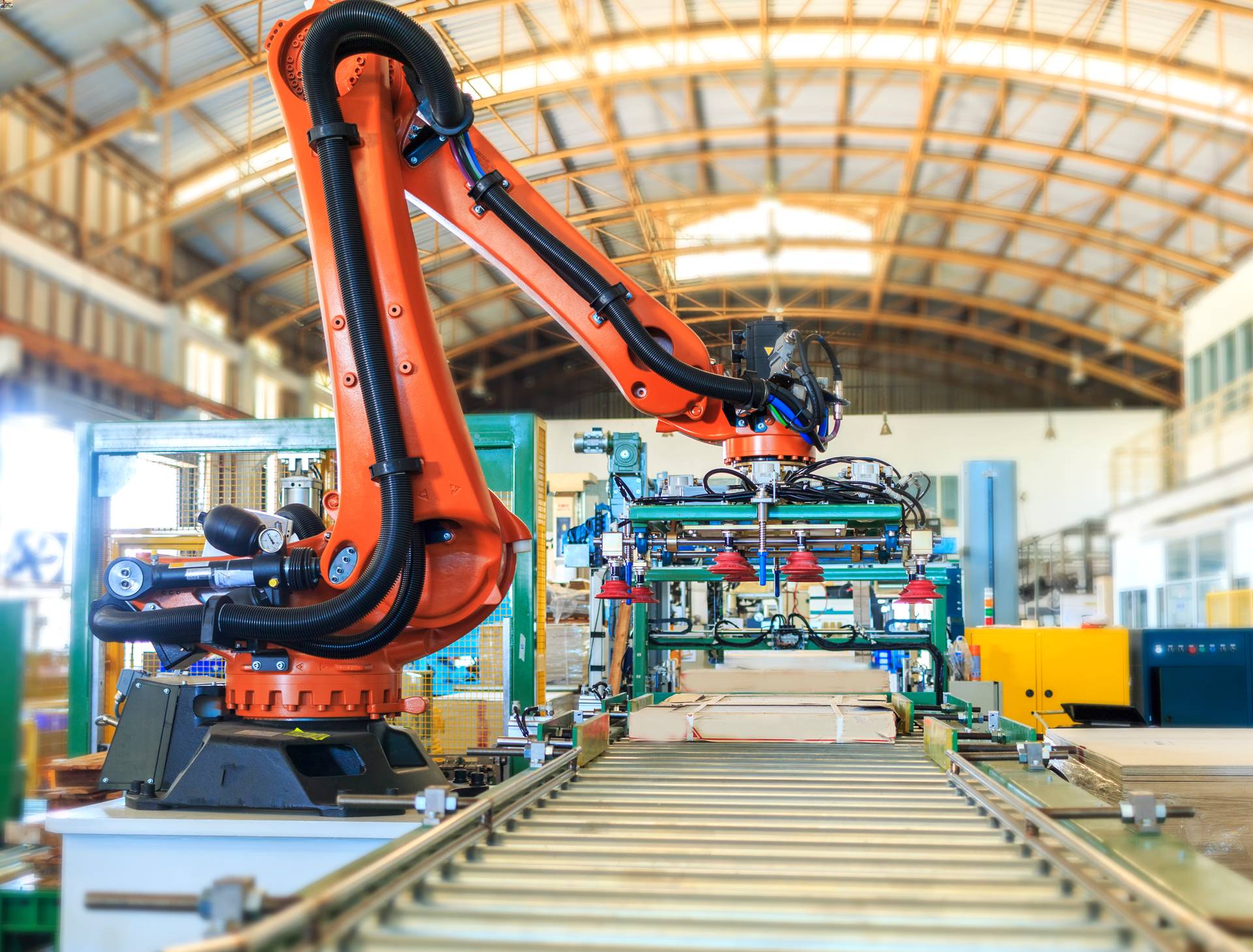
The futuristic tech here tends to fire the imagination— robots zipping around warehouses and using machine learning to fit items and palettes together like puzzle pieces. But behind the scenes on automation projects, HFA’s experts in electrical, mechanical, structural and fire-protection engineering quietly solve puzzles of their own. Their work can be critical to the safe, timely and cost-effective completion of DC and MFC automation projects.
Retailers can maximize results by bringing such experts into the conversation as early as possible. They also stand to benefit by consulting these architects and engineers whenever the MHE vendor makes changes to the initial design.
Break down silos
Frequent, clear and open communication is the key to running an efficient automation project, but sometimes this can require a conscious effort to break down silos between the different parties. For example, large retailers tend to have a certain division of labor: Their logistics experts give the MHE vendor clear goals for ramping up production at that DC or MFC. Generally, another part of that retail company—the engineering team—will procure the services of specialty firms like HFA. Our design work on these projects centers on making sure the new system are well coordinated and has the right power resources, compressed air, fireprotection coverage, structural supports and other elements related to the building and floorplan.
When these different divisions and subject-matter experts share information, ideas and plans from the outset, it can eliminate costly delays, frustrating headaches and, potentially, catastrophic failures.
On that latter score, our engineers have encountered designs in which…
- robots in motion would have knocked off sprinkler heads in the DC, potentially triggering an indoor “rain shower” that would have delayed production and ruined expensive inventory and equipment
- heavy ventilation fans would have kept running during a fire—literally fanning the flames— because they had not been wired into the fireprotection system in the initial design
- brief power outages of even a few seconds would have sent all robots back to home base to reboot, thus shutting down all warehouse throughput for up to four hours at a stretch—a problem remedied with installation of a backup power supply
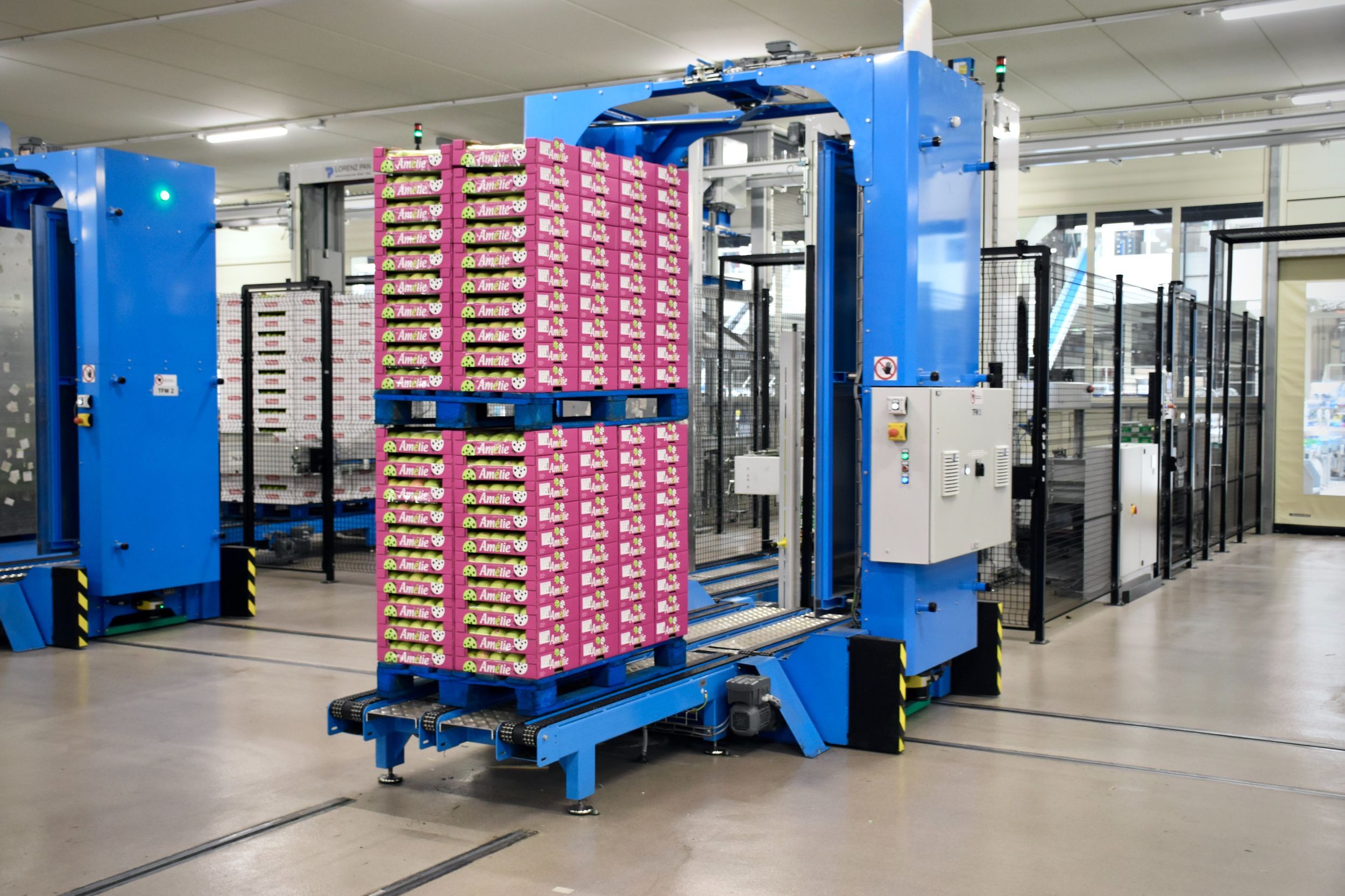
Been there, seen that
HFA engineers ask critically important questions on these projects: Does the layout of the equipment comply with existing fire-safety and ingress/egress codes? Does the design allow for the proper placement of additional electrical panels if a power upgrade becomes necessary down the line? Does the vendor’s 3D Autodesk Revit model leave out x-brace brackets or other elements that could get in the way of a robot or person moving through the space?
Our team of architects and engineers consult with utility and municipal officials to make sure their timetables for inspections and permitting align with the retailer’s planned schedule. Our teams prioritize communicating their deliverables and milestones and encourage other stakeholders to do the same— another best practice for smooth project coordination.
Powerful potential
Today’s DC and MFC automation systems are ramping up an array of logistics tasks. While some of our industrial sector clients have used conveyorbased systems to move packages for more than 20 years, new approaches to robotics and AI stand to transform logistics even more in the years ahead.
As more retailers bring “1.0” systems to their existing DCs, it will be more important than ever to have an experienced architectural and engineering team on hand, because new approaches always create additional puzzles in need of an effective solution. As we see it, on these complex, technical projects the “force multiplier” is not just years of experience—it is a deep commitment to the benefits of communication and collaboration.
Our architects and engineers may not be as fast as a robot-run MFC quite yet, but they are learning lessons and gaining speed with every successfully completed automation project.